半導体の重要性と製造工程の複雑さについて述べる
半導体は、現代のデジタル社会において不可欠な存在です。情報技術の急速な進化やエレクトロニクス製品の普及により、我々の日常生活は半導体によって支えられています。しかし、その製造工程は一般にはあまり知られていない複雑なプロセスであり、その深遠な技術と工学の融合には驚かされます。半導体の製造工程は、微細な構造や高度な技術を要求するため、非常に複雑です。
微細なパターンや層を作り出すためには、ナノメートル単位の精度が必要であり、その制御は極めて難しいものです。さらに、製造工程全体を通じて厳格な品質管理が求められます。
半導体製造工程は、デザイン段階から始まり、ウェーハ上に膜を形成し、パターンを転写し、最終的なデバイスを完成させるまでの一連の工程から成り立っています。この過程では、化学反応、物理的な加工、光学的な技術などが複合的に組み合わされます。
半導体の重要性と製造工程の複雑さは、現代のテクノロジー産業において欠かせないものです。その製造工程の奥深さは、常に新たな技術と革新によって前進しています。この分野での新たな発見と進歩は、私たちの生活や産業に革命をもたらす可能性を秘めています。
半導体とは?
半導体は、電気を伝導する能力があるが、導体(金属)ほどではなく、絶縁体(プラスチックなど)ほどでもない物質のことを指します。この中間の性質を持つため、現代の電子機器や通信技術において不可欠な素材として広く使用されています。
半導体の用途
半導体は、その特性から、電子デバイスの製造において重要な役割を果たしています。例えば、トランジスタやダイオードなどの基本的な電子部品から、集積回路(IC)や太陽電池、光ファイバーなど、様々な応用製品に利用されています。これらのデバイスは、情報技術や通信、エネルギー産業など多岐にわたる分野で利用されており、私たちの生活に深く浸透しています。
また、半導体の特性に基づいて、電気信号を制御したり増幅したりすることが可能です。このため、コンピュータやスマートフォン、テレビ、自動車の制御システムなど、さまざまな電子機器の中で重要な役割を果たしています。さらに、最近では人工知能(AI)やIoT(モノのインターネット)などの分野でも、半導体技術の進化が急速に進んでいます。
半導体は、その特性と応用範囲の広さから、現代のテクノロジー産業において中心的な役割を果たしています。電子機器や通信技術、エネルギー産業など、様々な分野で利用され、私たちの生活や社会を支える重要な素材として不可欠です。
半導体製造工程全体の流れ
半導体製造工程は、複雑で精密な工程が連続して行われるプロセスであり、高度な技術と厳格な品質管理が求められます。以下では、その工程全体の流れを概説します。
1. ウェーハの製造(Wafer Fabrication)
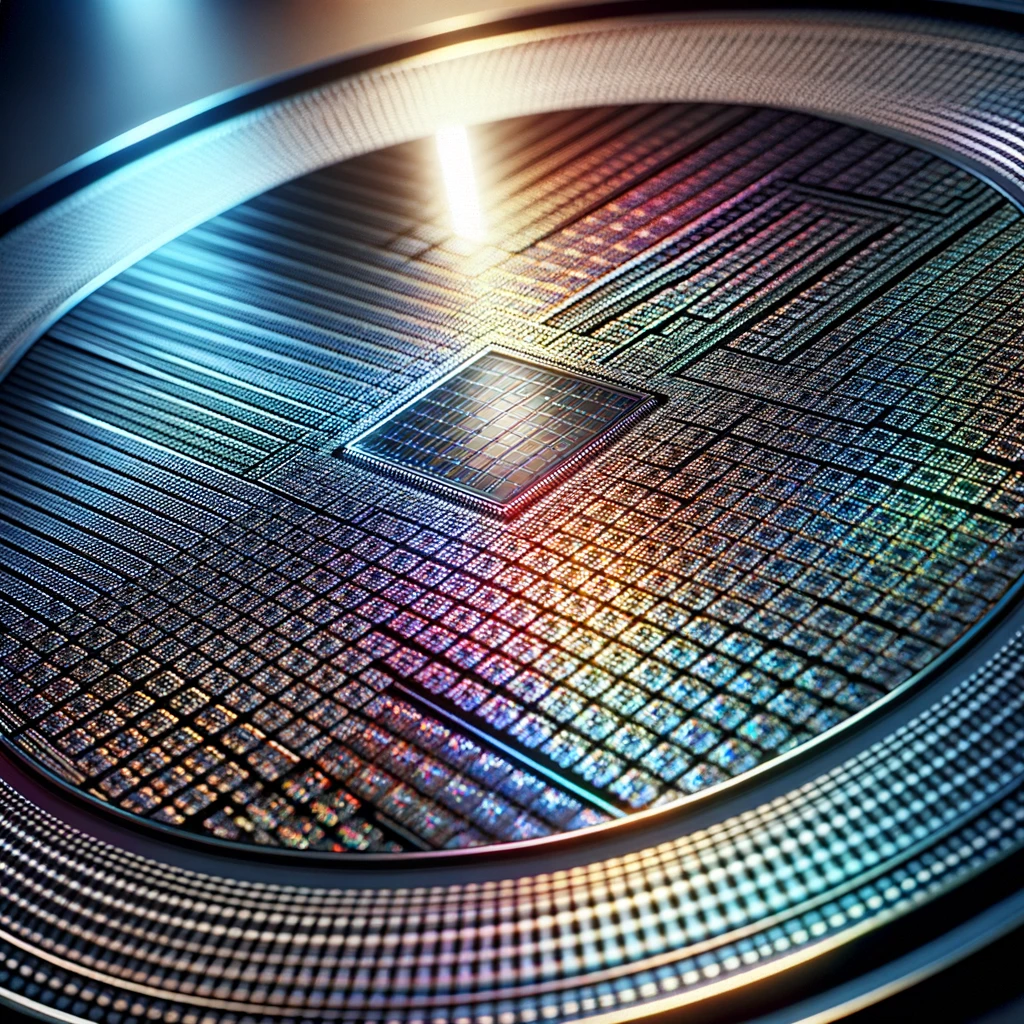
半導体製造の最初のステップは、ウェーハと呼ばれる基板の製造です。ウェーハは、非常に純度の高いシリコンを用いて作られた円盤状の基板であり、これが半導体チップの基盤となります。ウェーハの製造プロセスは、以下のような工程で構成されています。
1-1. シリコンインゴットの製造
最初のステップでは、シリコン原料を高温で溶かし、その後特定の結晶構造を持つように再結晶化させます。これにより、シリコンインゴットと呼ばれる大きな結晶塊が得られます。
1-2. インゴットの切断
次に、シリコンインゴットをダイヤモンド製のワイヤーソーを使用して薄い円盤状に切断します。これにより、ウェーハの原料となるシリコンディスクが作られます。
1-3. ディスクの研磨
シリコンディスクは、その表面が非常に滑らかで均一な厚さになるように研磨されます。この工程は、ウェーハの製造において表面の均質性と平坦性を確保するために非常に重要です。
1-4. ウェーハの洗浄
最後に、ウェーハは高度に洗浄され、表面から不純物や微粒子を取り除きます。これにより、ウェーハの純度が高まり、後続の製造工程での品質を確保します。
1-5. ウェーハ製造プロセスの要点
ウェーハの製造プロセスは、半導体製造の基盤となる非常に重要な工程です。高純度のシリコン原料からウェーハを製造することで、微細な電子機器の製造において必要な高い品質と性能を実現します。ウェーハの製造には、高度な技術と厳格な品質管理が必要であり、これらの工程が半導体産業の発展に不可欠な役割を果たしています。
2. ウェーハの薄膜形成(Thin Film Deposition)について
半導体製造において、ウェーハ表面に微細な薄膜を形成する工程は非常に重要です。この薄膜は、半導体デバイスの構造や性能を決定する上で欠かせない要素となります。ここでは、ウェーハの薄膜形成工程について詳しく見ていきます。
2-1. 薄膜形成プロセス
薄膜形成は、通常、化学気相成長(CVD)や物理気相成長(PVD)といった技術を用いて行われます。CVDでは、ウェーハ表面に原料ガスを供給し、熱やプラズマなどのエネルギー源を用いて化学反応を起こさせ、薄膜を形成します。一方、PVDでは、蒸着源から蒸発した材料をウェーハ表面に照射して薄膜を形成します。
2-2. 薄膜形成の制御
薄膜形成プロセスでは、薄膜の厚さ、均一性、結晶性など、さまざまな要素を制御する必要があります。特に、微細な半導体デバイスの製造では、ナノメートル単位の厚さや原子レベルの均一性が求められます。
2-3. 応用分野
ウェーハの薄膜形成は、半導体デバイスのほか、液晶ディスプレイや太陽電池など、さまざまな電子機器の製造にも応用されています。これらの応用分野では、異なる材料や薄膜の特性が求められるため、薄膜形成プロセスの技術開発が進んでいます。
まとめ
ウェーハの薄膜形成は、半導体製造において重要な工程であり、デバイスの性能や機能を決定する上で欠かせません。高度な技術と精密な制御が求められるこの工程は、半導体産業の発展に不可欠な要素となっています。
3. パターン形成(Patterning)
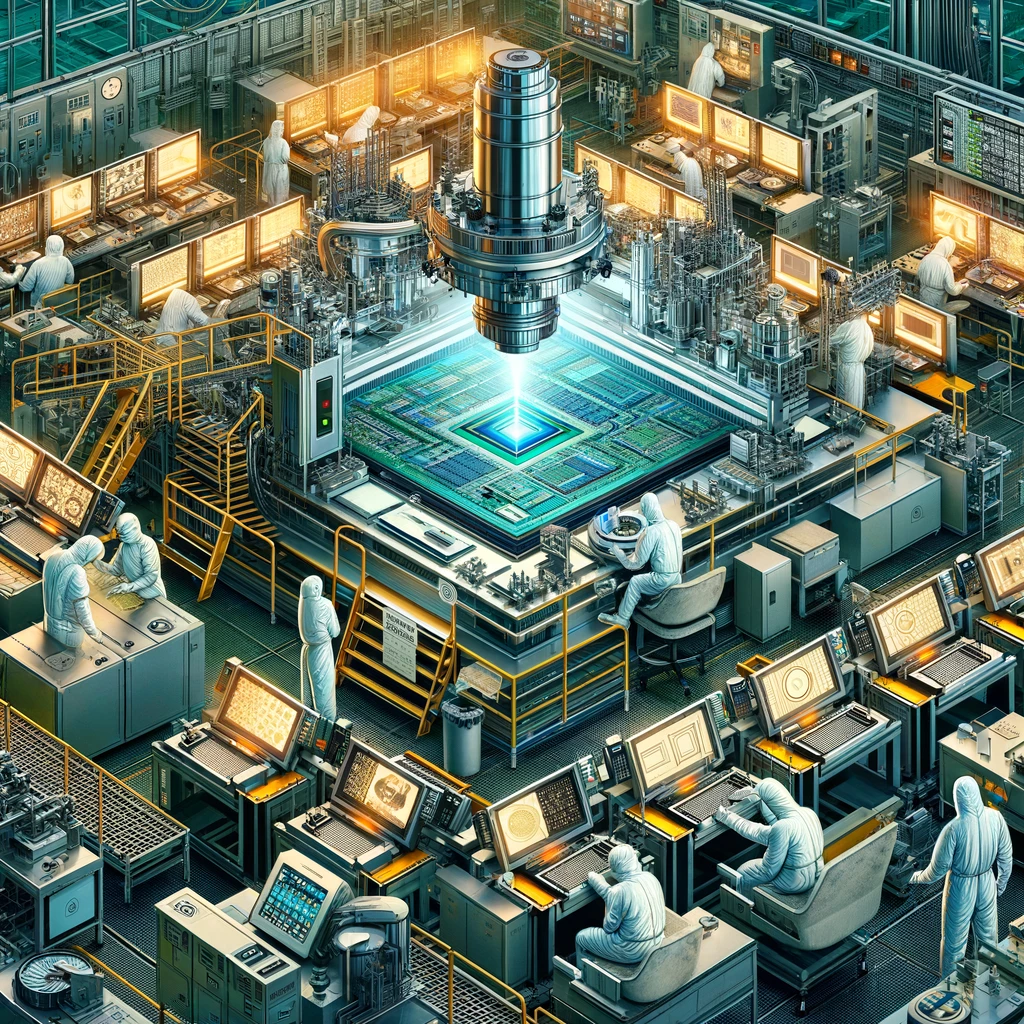
3-1. パターンとは
半導体製造工程におけるパターンとは、ウェーハ表面に形成される微細な模様や構造のことを指します。これらのパターンは、微細な線や穴などの形状を持ち、それぞれの半導体デバイスの機能や回路を構築するために必要です。
3-2. パターン形成プロセス
パターン形成は、主にフォトリソグラフィと呼ばれる技術を用いて行われます。このプロセスでは、フォトマスクと呼ばれるマスクを使用して、光を照射し、ウェーハ表面に所定のパターンを形成します。フォトレジストと呼ばれる感光性の材料をウェーハに塗布し、その上にフォトマスクを配置して光を照射することで、パターンが転写されます。
3-3. パターン形成の重要性
パターン形成は、半導体デバイスの微細な構造を作り出すために非常に重要です。この工程で形成されるパターンの精度や解像度が高ければ高いほど、デバイスの性能や機能が向上します。したがって、パターン形成プロセスの制御と技術革新は、半導体産業の発展に不可欠です。
4. エッチング(Etching)
半導体製造工程におけるエッチングとは、ウェーハ表面の一部を特定のパターンや形状に削り取るプロセスです。この工程は、フォトリソグラフィによって形成されたパターンを基に、不要な部分を除去することで、微細な構造を形成するために行われます。
4-1. エッチング方法
エッチングには、化学的エッチングと物理的エッチングの2つの主要な方法があります。化学的エッチングでは、特定の化学溶液(エッチング液)を用いてウェーハ表面を削り取ります。一方、物理的エッチングでは、プラズマなどの高エネルギー粒子を用いてウェーハ表面を除去します。
4-2. エッチングの重要性
エッチングは、半導体デバイスの微細な構造を形成するために極めて重要な工程です。正確で精密なエッチングは、デバイスの性能や機能を決定するために不可欠です。また、エッチングプロセスの制御によって、微細なパターンや構造を実現し、半導体デバイスの性能を向上させることが可能です。
5. インプラント(Ion Implantation)
半導体製造工程におけるインプラントとは、イオン注入とも呼ばれ、ウェーハ表面に特定のイオンを注入するプロセスです。この工程は、半導体素材の導電性や電気的特性を変化させ、デバイスの動作や性能を調整するために行われます。
5-1. インプラント方法
インプラントは、高エネルギーを持つイオンビームをウェーハ表面に照射することで実現されます。イオンビームがウェーハ表面に衝突することで、ウェーハ内部にイオンが挿入され、半導体素材の特性が変化します。このプロセスは、微細な領域に対して高い制御性と精度を持って行われます。
5-2. インプラントの重要性
インプラントは、半導体デバイスの動作や性能を制御するための重要な工程です。特定のイオンを注入することによって、ウェーハ内部の導電性やドープ濃度を調整し、デバイスの動作速度や電流の流れ方などを微調整することが可能です。これによって、半導体デバイスの性能向上やエネルギー効率の向上が実現されます。
6. 金属配線形成(Metalization)
半導体製造工程の金属配線形成は、半導体デバイス内の異なる部品や回路を接続するための重要な工程です。この工程では、導電性の高い金属材料を使用して、微細な配線パターンを形成し、各部品や回路を結びつけます。これにより、半導体デバイスの信号伝達や電力供給が可能になります。
6-1. 金属配線形成のプロセス
金属配線形成のプロセスは、まず、ウェーハ表面に薄い金属膜を形成します。次に、光やエッチングなどの方法を使用して、必要な配線パターンを定義します。その後、不要な金属を除去するエッチング工程を行い、最終的に必要な配線パターンが残ります。このようにして、微細な金属配線が形成され、デバイス内の各部品や回路を効果的に接続します。
6-2. 金属配線形成の重要性
金属配線形成は、半導体デバイスの機能性や性能に直接影響を与える重要な工程です。正確な配線パターンの形成と高い導電性を持つ金属材料の選択によって、信号の伝達速度や電気的特性が向上し、デバイスの性能が向上します。また、微細な配線パターンを形成することで、デバイスのサイズを小さくし、高集積化を実現することも可能になります。
7. テストと検査(Testing and Inspection)
半導体製造工程におけるテストと検査は、製造された半導体デバイスが仕様に適合しているかどうかを確認するための重要な工程です。これにより、製品の品質や信頼性を確保し、不良品を排除して市場に出荷することが可能になります。テストは製品の機能性を評価し、検査は製品の外観や物理的な特性を確認します。
7-1. テストと検査のプロセス
テストと検査のプロセスは、製品の種類や用途によって異なりますが、一般的には以下のステップで行われます。まず、製品に電気信号やテストパターンを適用して、機能や性能を評価します。次に、製品の外観や寸法、配線などを目視や機器を使用して検査し、不良箇所を特定します。最後に、不良品を修正するか廃棄し、品質管理の観点から検査結果を記録します。
7-2. テストと検査の重要性
テストと検査は製品の品質を確保する上で欠かせない工程です。製品が仕様に適合しているかどうかを確認することで、市場に出荷された製品が顧客の期待に応えることが可能になります。また、不良品を早期に発見し修正することで、生産効率の向上やコストの削減にも貢献します。さらに、テストと検査によって製品の信頼性を確保し、長期間安定した動作を実現します。
設計
半導体製造工程の設計は、製品の機能や性能を決定する重要な段階です。この工程では、製品の要件や仕様に基づいて、回路やレイアウトの設計が行われます。設計段階では、CAD(Computer-Aided Design)ツールやシミュレーションソフトウェアを使用して、回路の配置や配線パターン、トランジスタの配置などを最適化します。設計段階での適切な計画と設計は、製造工程全体の効率と品質に直接影響を与えます。
設計するもの
設計するものは、主に以下の要素に関連します。
回路設計(Circuit Design)
導体デバイスの機能を実現するための回路を設計します。これには、論理回路、アナログ回路、ミックスドシグナル回路などが含まれます。
レイアウト設計(Layout Design)
設計した回路を実際のチップ上に配置するレイアウトを設計します。配線の配置やサイズ、間隔などが検討されます。
物理設計(Physical Design)
レイアウト設計をより具体的な物理的な制約に基づいて最適化します。これには、配線の長さや幅、積層の方法などが含まれます。
シミュレーション(Simulation)
設計段階で、回路やレイアウトの挙動をシミュレーションして機能や性能を評価します。これにより、製品の性能や信頼性を事前に検証することができます。
まとめ
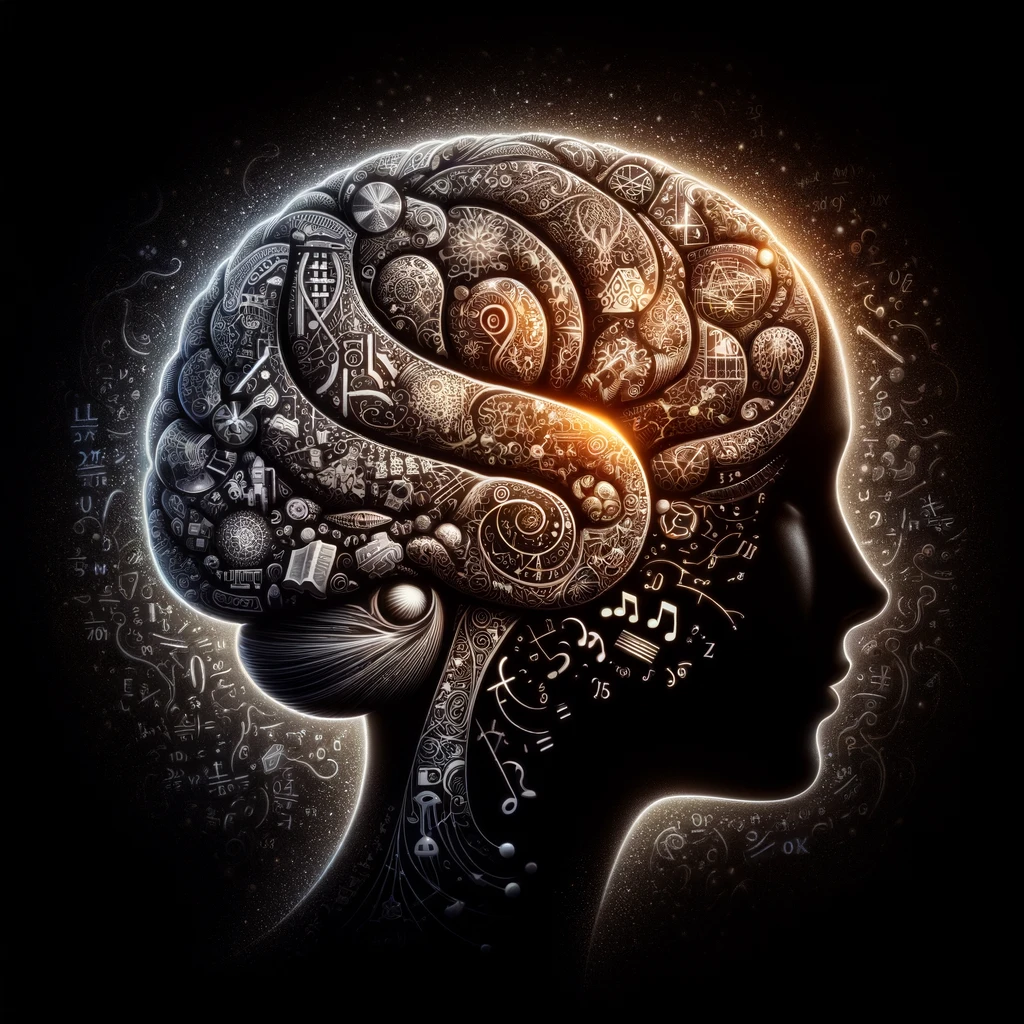
半導体製造工程は、微細な技術と厳格な品質管理が要求される複雑なプロセスです。ウェーハの製造から始まり、前工程、パターン形成、エッチング、金属配線形成、最終的なテストと検査まで、各段階で精密な手順が重要です。これらの工程を通じて、高性能で信頼性の高い半導体が生み出されることがわかると思います。この記事でより興味持ってくださると幸いです。以上。
コメント